型板
銅板を焼き鈍して所定の形に成型するためには型板と当て板が必要です。ボイラー作製の本には、堅木で型板を作れば大丈夫と書いてあるが、6台作るとなると型が変形してしまうので金属で作らなければなりません。厚い鉄板でなければ意味がないので探して見つけたのが、工事現場でぬかるんだ場所でもトラックが入れるように敷く厚さ15mmの鋼板でした。この鋼板がとんでもなく硬く、小さく切り分けるのに酸素で溶断しなければならないくらいでした。
切り出した鋼板を所定の形にバンドソー、サンダ、ヤスリを駆使して概形を形成し、フライスで仕上げました。鏡板の型板はパイプとパイプを繋ぐ継ぎ手(フランジ)に寸法が合ったものがありそれを利用しました。
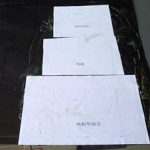
PCで打ち出した図面をトタン板に張り付け切り出して罫書き用の治具として使用
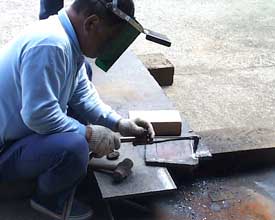
鋼板が大きく、硬いので酸素で切断
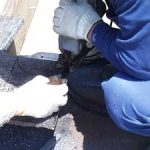
喉板部分をジグソーで切断
銅板の打ち出し
銅板を所定の形よりも少し大きめにカットし、バーナーで焼き鈍し、型板とそれより板厚分だけ大きめにした当て板の間に焼き鈍した銅板を挟み込んで万力で固定します。プラスチックハンマーや木槌、銅ハンマーなどを使い分けて数回たたくと硬くなるので万力からはずし、再度焼き鈍します。硬いままたたき続けるとひび割れが生じる恐れがあり、だめになるので加熱してひずみを取り除き、型板、当て板に挟んで万力で締めてたたく、これを設計寸法になるまで何回も繰り返す訳です。
銅板は加熱した後に急冷しても焼き鈍しの程度は変わらないので、急ぐ場合は急冷してもよいが、我々は大量生産なので焼き鈍しと打ち出し作業を分担し、流れ作業で行うので徐冷しながら作業しました。
内火室管板、内火室後板、外火室後板などは簡単だが、喉板部分は型板が2枚という複雑な形態をしているので打ち出しには、銅板の当て方を慎重にしないと打ち出した後の寸法が足らないということになりかねません。
煙室管板の当て板は既製のフランジを利用したが、管板の外径は150mmなので、ちょうど内径150mmのフランジがあったのでそれをジグにして通すと、絶妙の仕上がりで缶胴をふわふわとゆっくり落ちていく出来でした。
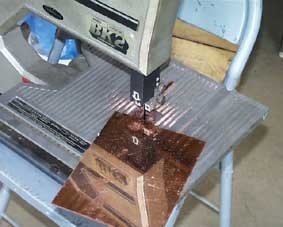
銅板の切り出し
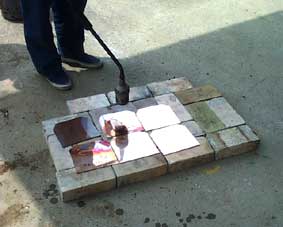
6枚並べて焼き鈍し
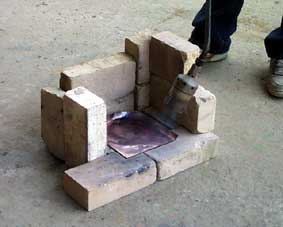
型板に当てて少したたくと硬くなるため再焼き鈍し
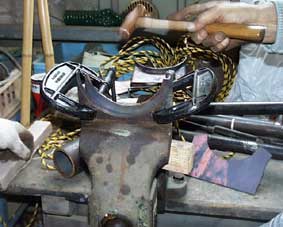
喉板の打ち出し
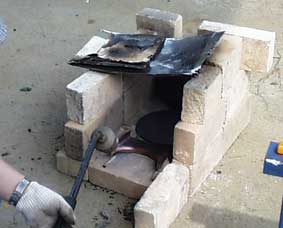
喉板の焼き鈍し
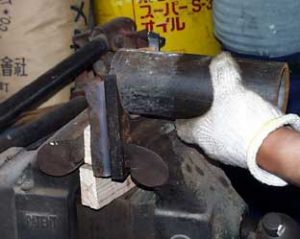
凹面のため鉄管を当ててたたく
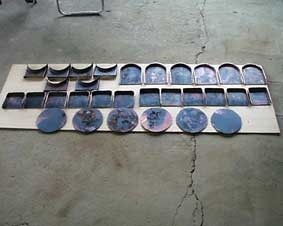
ここまで出来ました
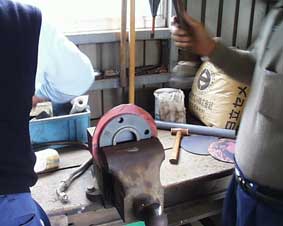
フランジに当てて煙室管板の打ち出し
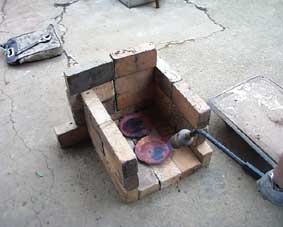
再焼き鈍し